DRY FILM LUBE
DRY FILM LUBRICANT (DFL)
Our Dry Film Lube technologies, or DFL, are waterborne coatings that form a hard, dry-to-the-touch, temporary film that provides significant lubricity for metal forming without the need for wet lubricants.
- Eliminates the need for oils and other drawing compounds
- Compatible with all metal substrates
- Eliminates metal-to-metal contact protecting the tool, die, and formed part
- Provides temporary transportation corrosion protection
- Increases plant efficiency, decreases scrap loss and prolongs tool & die life
- Ideal for deep-draw stamping
- Removable after forming
- Does not affect secondary processing (Slitting, CTL, etc.)

Industries We Serve
We offer DFL products for every substrate, including HRS, CRS, Galvanneal, Aluminized, HDG, EG, Aluminum (various grades), and stainless steel (various grades). Additionally, our InterCoat® ChemGuard products can be utilized as a permanent dry film lubricant for galvanized substrates – allowing for the elimination of lubricants while providing extensive corrosion resistance.
BENEFITS OF DRY FILM LUBE
Dry Film Lubricant eliminates the need for oils, pre-lubes, and other compounds that are currently used to aid in the stamping and forming process. DFL is an environmentally safe choice that saves money, reduces scrap and improves part quality.
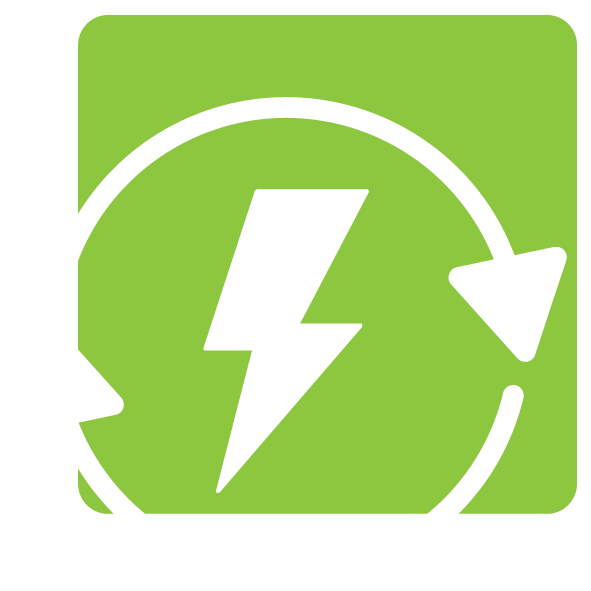
PLANT EFFICIENCY
DFL improves productivity and efficiency by decreasing die maintenance and the need to clean during runs. You’ll need fewer die adjustments during long runs, and can skip steps for rust preventatives and washing before welding and sampling.
Overall, DFL can cut seconds off every single piece, leading to fewer run hours and increased capacity.
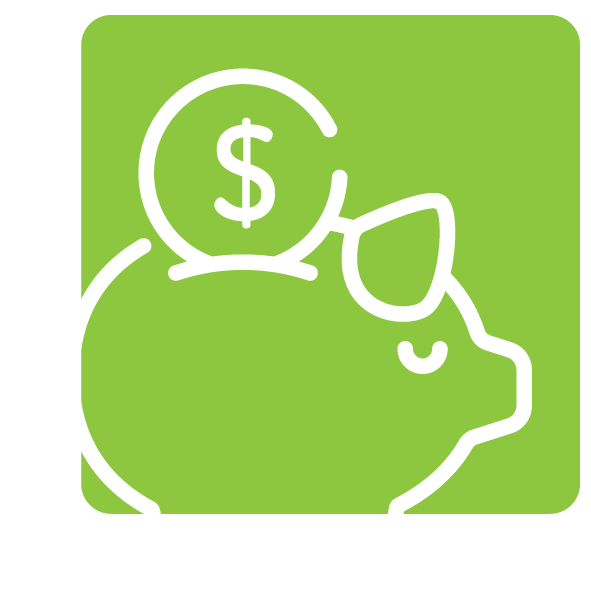
COST SAVINGS
Eliminating metal-to-metal contact means dies last longer, lower scrap rates, and longer tooling life. Without the mess of wet lubricants, DFL also reduces facility cleaning costs and safety hazards.
DFL also improves substrate formability, eliminating surface reconditioning. That means spending less on lower-grade steel without quality loss.
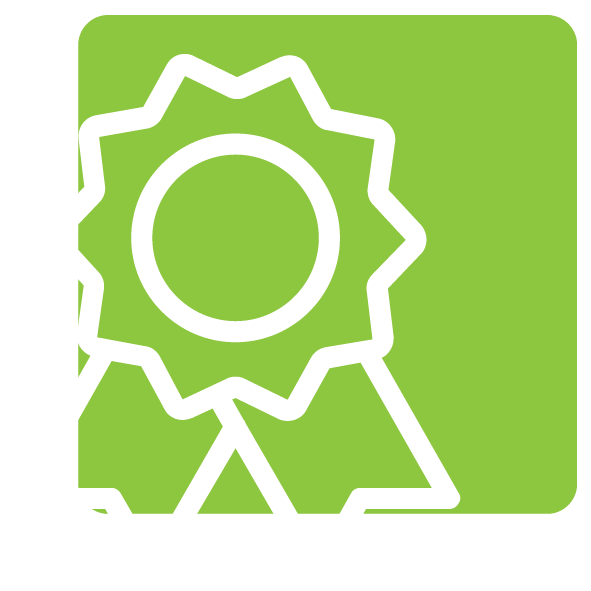
PART QUALITY
Better tooling and part protection leads to consistent, defect-free products with better definition, reduced edge burrs, and less galling.
DFL also offers temporary corrosion protection through processing. It can be removed by a standard alkaline cleaner after forming, and in some cases can be left on the metal as used as-is.
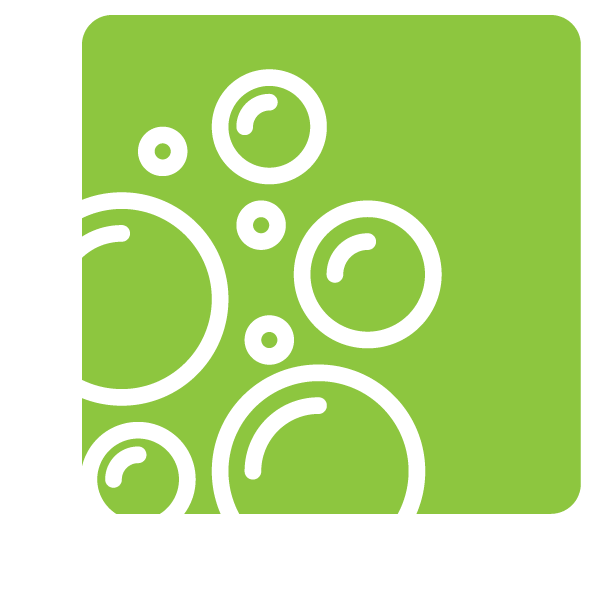
CLEAN ENVIRONMENT
DFL eliminates the amount of regulated reporting by removing VOCs and HAPs from the process. It supports our environmentally-friendly mission by reducing respiratory and fire safety risks associated with wet lubricants.
As an added plus, it also eliminates oil storage, freeing up square footage for other uses.
Let’s Connect
Connect with a sales representative today. Let’s talk about engineering a solution for you.