ASTM B117 Salt Spray Tests have only a loose correlation to real-world conditions. No rainstorm (especially one carrying heavy salt concentrations) continues, unstopped, for hundreds of hours. The real world works more like cycle testing: stop the weather, let it dry, hit it again. The correlation to real-world durability is never entirely precise, but either test achieves one-to-one predictability down to an exact month.
The tests do have some value for testing relativity. If two materials are subjected to the same stress at the same time, it’s possible to say that one is better at withstanding that particular condition than the other. Say a couple pieces of galvanized metal are cut, perforated and scratched; if one rusts on the cut edge, on the edge of the perforation and on the scratch, and the other (say, the one with InterCoat®ChemGuard) does not, the best that can be said is on all those tests, the second one clearly outperforms the other.
Even on a relative basis, it’s interesting when a substantial difference in performance can be seen between two tests. We tested a piece of HDG G235 (see graph below) and a comparable piece of metal with InterCoat®ChemGuard. The piece of HDG G235 was completely covered with red rust after testing, while the InterCoat®ChemGuard, on the other hand, was run for nearly twice as long with no rust. It seems clear that, regardless of the methodology of the test itself, there’s a clear level of superiority of the InterCoat®ChemGuard.
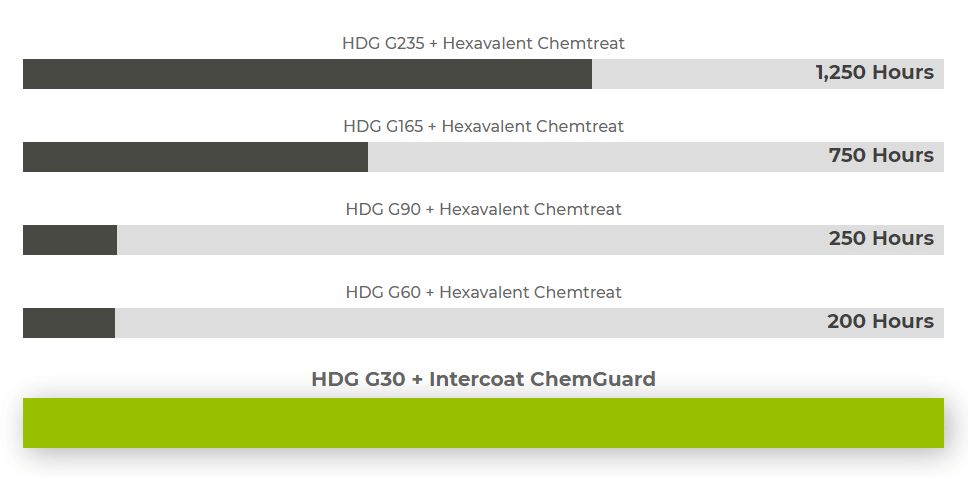